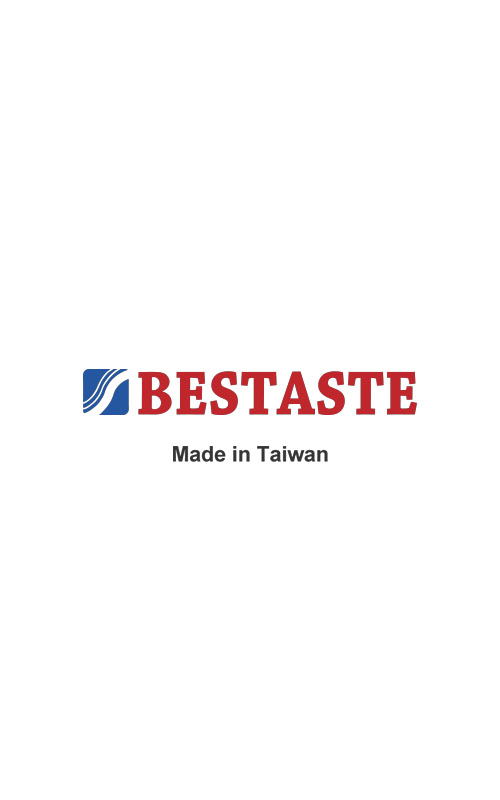
At Bestaste, our automatic spring roll machines are not only built with precision engineering and advanced technology but are also known for their exceptional performance and reliability. They are ideal for various types of food production businesses. The key components of a spring roll making machine typically include:
Machine System Overview
The machine system is divided into two main sections, each responsible for a distinct stage in the spring roll production process:
Section 1: Spring Roll Wrapper Production machine
This machine handles the automated production of spring roll wrappers. The process includes:
Batter Supply and Coating: A batter supply system evenly applies the prepared batter onto a rotating heated drum, forming a thin and uniform wrapper layer.
Heating and Forming: Through precise temperature control, the batter is quickly cooked and solidified into complete spring roll sheets.
Wrapper Conveying: The finished wrappers are then transferred via conveyor belts to the next processing stage.
Section 2: Cutting, Filling, and Forming
This machine processes the wrappers into finished spring rolls through the following steps:
Precision Cutting: The wrappers are accurately cut into standard sizes after proper positioning.
Filling: A precise filling system deposits a measured amount of pre-prepared filling (typically shredded vegetables, meat, or noodles) into the center of each wrapper.
Automatic Folding and Rolling: A multi-step mechanical process folds and rolls the wrapper around the filling, forming the spring rolls. The completed products are then conveyed for packaging or cooling.
Next, we will provide a detailed description of the unique features of these two units as designed by Bestaste.
Spring Roll Wrapper Production machine
1. Batter Feeding System:
At Bestaste, we prioritize durability and performance. Our spring roll pastry machines use stainless steel gear pumps to deliver the batter to the forming nozzles. Unlike plastic or polymer gears, stainless steel offers significantly longer service life and consistent performance under high-volume operation. This choice reflects our commitment to quality and reliability—not just cost-cutting. By investing in premium materials, we ensure that every part of the machine upholds the highest standards in food machinery manufacturing.
2. Forming Nozzle System:
Our specially engineered forming nozzles are a key innovation in Bestaste’s spring roll wrapper production process. These nozzles are crafted using a proprietary technique that allows users to easily adjust the thickness of the wrapper according to their specific requirements. The result is a uniformly smooth and flat sheet, without raised edges—ideal for consistent wrapping and presentation.
Additionally, our nozzle design effectively reduces issues commonly caused by fine particles in the batter, such as breakage or uneven flow during production. The nozzle structure is optimized to prevent clogging at the outlet, ensuring a stable and continuous flow even when the batter contains small granules. This translates into fewer production interruptions, improved efficiency, and higher yield quality.
3. Heating and Drum System:
Once the batter is dispensed through the forming nozzle, it lands onto the heated rotating drum, where it is baked into a thin, uniform spring roll wrapper. At Bestaste, we offer two types of drum surfaces to accommodate different product textures and thickness requirements:
A: Smooth Surface Drum:
Ideal for producing ultra-thin wrappers as thin as 0.32mm, this surface ensures a sleek, even finish. Some customers prefer this type of drum specifically for making exceptionally thin spring roll wrappers, depending on their product style and market preferences.
B: Rough Surface Drum:
Designed for slightly thicker wrappers (minimum 0.4mm), this drum features a roughened surface that creates micro-perforations on the wrapper. These tiny holes enhance the crispiness of the spring roll after frying, making it a preferred choice for products aiming for a crunchy bite.
Advanced Heating System:
Our heating system uses a specially designed method that allows the heat from the heater to be transferred more efficiently to the drum. In many other machines, heaters are easily damaged because the heat they produce is not transferred well, causing them to overheat and fail. At Bestaste, we have solved this problem by improving the way heat is spread, making sure the drum heats evenly and the heater lasts longer.
The heater is covered with high-insulation thermal wraps, directing heat outward and minimizing energy loss.
We customize the heater size based on the target wrapper size, ensuring even temperature distribution across both the center and edges of the wrapper. This results in consistent baking and wrapper quality.
High-Quality Internal Components:
Inside the drum, we use pure nickel resistance wires, known for their excellent high-temperature tolerance and stability. This premium material choice ensures long-term operational stability and further reflects Bestaste’s commitment to quality over cost-cutting.
Spring Roll Wrapping Machine
After the spring roll wrappers are produced, the wrapping process is carried out by our automatic spring roll wrapping machine, which is composed of three main sections:
Wrapper Cutting System
The continuous spring roll sheet is precisely cut into individual wrapper pieces. Cutting length can be adjusted based on the desired spring roll size. This ensures consistent dimensions and prepares each piece for efficient filling and wrapping.
Filling System
A synchronized filling mechanism dispenses pre-cooked or chilled fillings (such as vegetables, meats, or noodles) directly onto each wrapper. The filling volume can be adjusted to suit different product specifications. The system is designed to maintain even distribution and minimize mess or leakage, improving overall product consistency.
Folding and Rolling System
After filling, the wrapper is automatically folded and rolled into a tight, uniform spring roll. The machine mimics traditional hand-folding methods, ensuring the spring roll is securely sealed and maintains a neat, compact shape—ready for frying, freezing, or packaging.
Key Advantages of Bestaste Spring Roll Machines
High Efficiency:
Capable of producing up to 2,400 spring rolls per hour, with customizable roll size and shape (round or flat) available according to production requirements. Dimensions such as length, weight, and form can be configured to match specific product needs during the setup phase, offering flexibility for a wide range of applications.
Exceptional Durability:
The entire machine is constructed from high-grade stainless steel that meets FDA and CE standards, ensuring long-term hygiene and structural stability. Our baking drums and heating elements are built with durability in mind, using carefully selected materials and proven engineering designs that extend their service life significantly compared to standard components. Bestaste machines are designed to operate reliably for many years, even under high-volume production conditions.
Versatile Customization:
At Bestaste, we believe no two products are exactly the same. That’s why we offerhighly flexible customization services, tailored to meet even the most specific requirements. Over the years, we’ve helped clients produce spring rolls with unique specifications—including wrappersas wide as 4 cm, rolls only 6.5 cm in length, and even productsweighing just 15 grams. Whatever your product concept may be, our engineering team works closely with you to bring it to life with precision and reliability.
Energy-Saving by Design:
Bestaste’s spring roll wrapping machine is powered by a single motor that drives 21 precisely coordinated cam plates. This intelligent mechanical system replaces the need for multiple electronic actuators and complex control circuits, enabling smooth, synchronized operations with significantly lower energy consumption.
By relying on cam-driven mechanics, the machine offers several key advantages: it is less susceptible to water damage, requires minimal maintenance, and delivers highly reliable performance even under continuous production. This design reflects Bestaste’s commitment to long-term efficiency, stability, and operational simplicity.
Premium Components:
Bestaste machines are built with internationally recognized components, including SIEMENS motors (Germany) and Fuji Electric parts (Japan). These trusted global brands are well-known for their reliability, stability, and performance, ensuring that our machines can operate smoothly and consistently in diverse production environments around the world.
FDA-Compliant Frame:
The frame is built with 5mm and 10mm thick stainless steel plates, ensuring excellent structural strength, rust resistance, and deformation protection. All food-contact surfaces and machine structures are designed following FDA sanitary design guidelines, making them easy to clean and maintain in compliance with international food safety standards.
At Bestaste, we don’t just build spring roll machines—we provide solutions that are reliable, customizable, and built to last. From our precision-engineered heating systems to our cam-driven wrapping technology, every detail is designed with performance, hygiene, and longevity in mind.
Whether you're scaling up production or creating a unique product line, Bestaste machines are built to support your goals with confidence and consistency.
Let us help you turn your ideas into reality.
If you have any questions or specific requirements, our team is always ready to provide expert advice and support tailored to your needs.